Benefits of BIM: Collaborating to Improve Cost Analysis
How can the BIM approach significantly improve the cost analysis of projects?
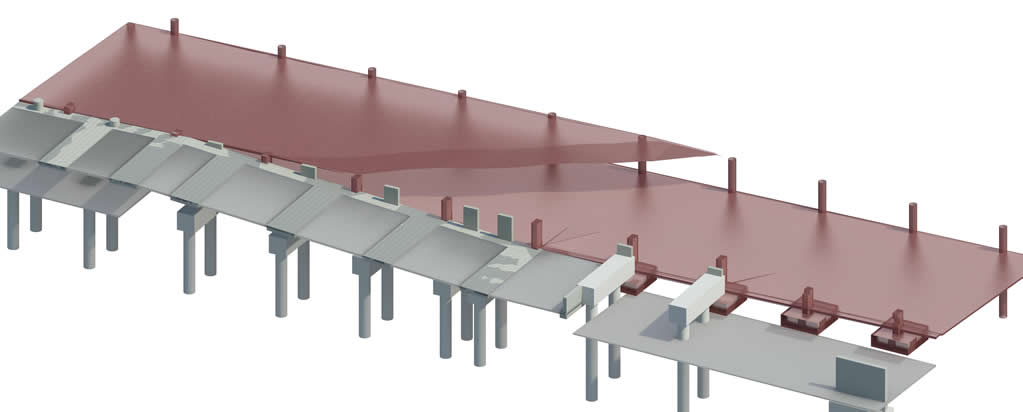
For BIM to work, sharing knowledge and expertise in order to empower collaborative thinking is paramount. The benefits of close collaboration between the architects and engineers or architects and contractors has been well explored but Meinhardt and quantity surveyors Rider Levett Bucknall (RLB) are now demonstrating to clients how the BIM approach can significantly improve the cost analysis of projects.
The team is currently working on an $80 million basement carpark and 15,000 square metre commercial office development. The complexities and potential risks around a project of this scale can be significant.
The Meinhardt and RLB team therefore wanted the ability to identify costly construction items at an early stage for the client so that they could allocate appropriate allowances against these risks or provide a platform to suggest alternative, more efficient design solutions.

Model View inside Proposed Carpark highlighting area of Existing Footing Interface
They needed a faster, more efficient and more accurate way to confidently extract quantities, particularly on complex structure elements such as podiums and transfer floors.
Using BIM technology reduced the time spent doing manual measurements so that more time could be spent analysing data against benchmark information to provide valuable feedback to the design team regarding building efficiencies.
RLB was able to dynamically link models to the cost plan for more frequent updates allowing early notification to the team if the design is on budget at an earlier stage, rather than just after project milestones such as the schematic design or design development stages.
Meinhardt has worked closely with RLB to provide them with a detailed knowledge of the ‘nuts and bolts’ of REVIT modelling and its database to accurately map data to their costing software. By giving the QS intimate knowledge of their models and modelling techniques, including transparent, unbiased advice, the engineers have been able to highlight inaccuracies through software limitations or modelling exclusions and provide a robust, fully-zoned and managed model which accurately maps the building elements to the cost plan.
The detailed models, audited under a Meinhardt developed Model Management checking process, also contain additional parametric data, which maximises the amount of bulk quantification that can be processed by RLB on the project.
“Actively engaging with the QS and promoting transparent knowledge sharing is paramount,” said Meinhardt BIM model manager Barry Orr. “Design Teams should be starting to understand the benefits of involving the QS in the initial BIM start-up meetings. To date, designers have been nervous that the QS will require additional model information outside their scope and have subsequently shied away from fully engaging with them during the BIM design process.”

Barry Orr, BIM Model Manager at Meinhardt delivers a BIM training seminar
He said Meinhardt implement several engagement initiatives from the get-go.
“By holding meeting room seminars, producing BIM guidance documents & Video Tutorials, this allowed RLB to quickly identify the means of how they would accurately quantify each element of the project,” he said. “We knew it was not good enough just to then simply issue a model to the QS and leave them to it. We therefore continued to actively work alongside RLB after the model delivery too, ensuring continuous improvement.”
The result now is that both RLB and Meinhardt have an intimate knowledge of the mechanics of each other’s software. This gives them the ability to provide highly efficient, fully costed designs solutions in a shorter period.
RLB has been able to quickly identify high-risk cost items on the project and provide immediate feedback to the team. For example, through modelling the existing building in 3D, the team was able to quickly identify that some existing foundations of the neighbouring building, which was not due for demolition, would require underpinning due to the interface with the new basement carpark levels. RLB was able to accurately quantify the works required and the team were able to quickly redesign the area to suit the most cost effective solution to maximise the efficiency of the basement carpark.
“Due to our close working relationship & understanding of each others software, processes & modelling techniques, we were able to add value by being more pro-active in the realisation of better design solutions. Without this working relationship, the benefits and efficiencies will not be realised,” said Rider Levett Bucknall senior QS Allan Trotter.

View of imported structural model when imported into RLB’s Costing Software
LOOKING INTO THE FUTURE
The barriers to be overcome in the foreseeable future include:
- Client adoption of the opportunities in BIM
- Establishing industry standards and protocols throughout the design, construction and facility management
- Early adoption of BIM in the design process
- Industry education and awareness
This article was originally posted on Design Build Source